When Experience Matters!
At Williams, we believe selling a product is more than an exchange of tools. When you work with Williams, you work with heavy-duty tool professionals whose experience in the field and the factory help you make smart decisions for your business.
Our experts are available to train your associates on the importance of using a product safely and using the right tool for the job and the importance of tool maintenance. We offer solutions to improve productivity through various product solutions. We recognize the need to get work done better, faster and more safely.
With demanding timelines, unusually tough conditions and many other obstacles businesses face today, it is important to partner with a company that understands your challenges. Williams and our distributors are here to help you find the right solutions for your individual business. Williams has a network of professionals with knowledge you can count on.
We provide value before, during and after the sale that you can trust. When you are looking for a partner to help streamline your processes, contact us today to meet with one of our experts.
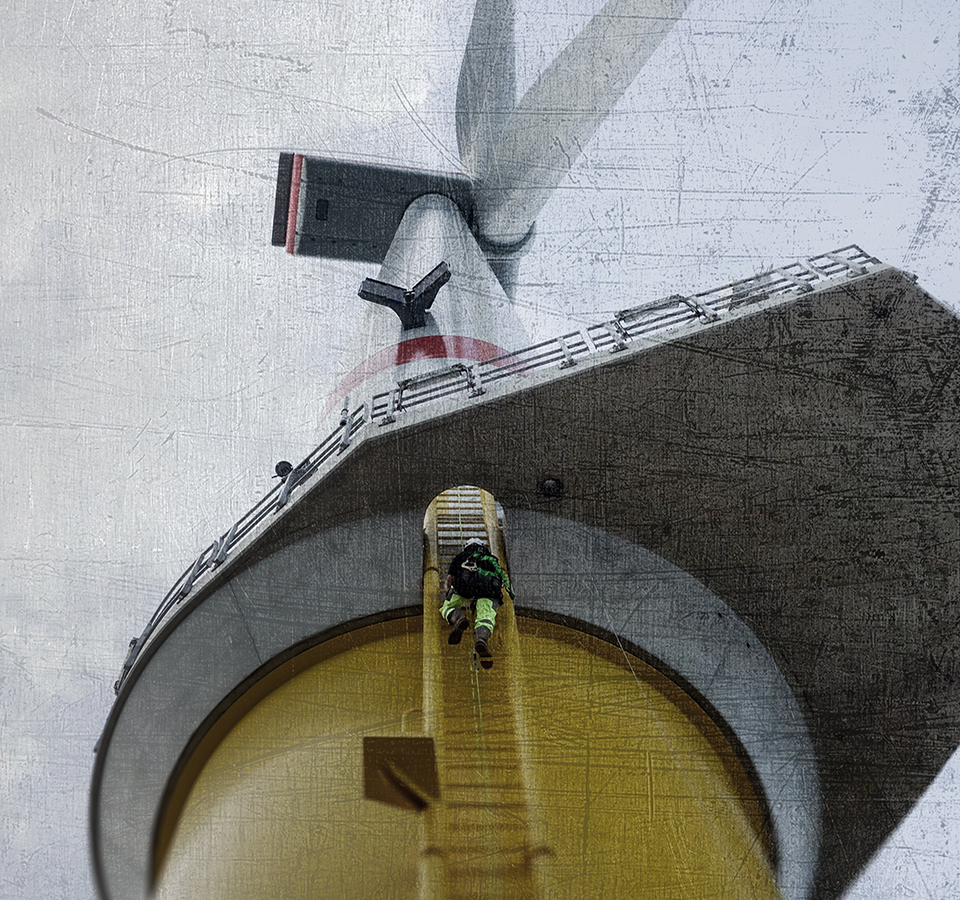
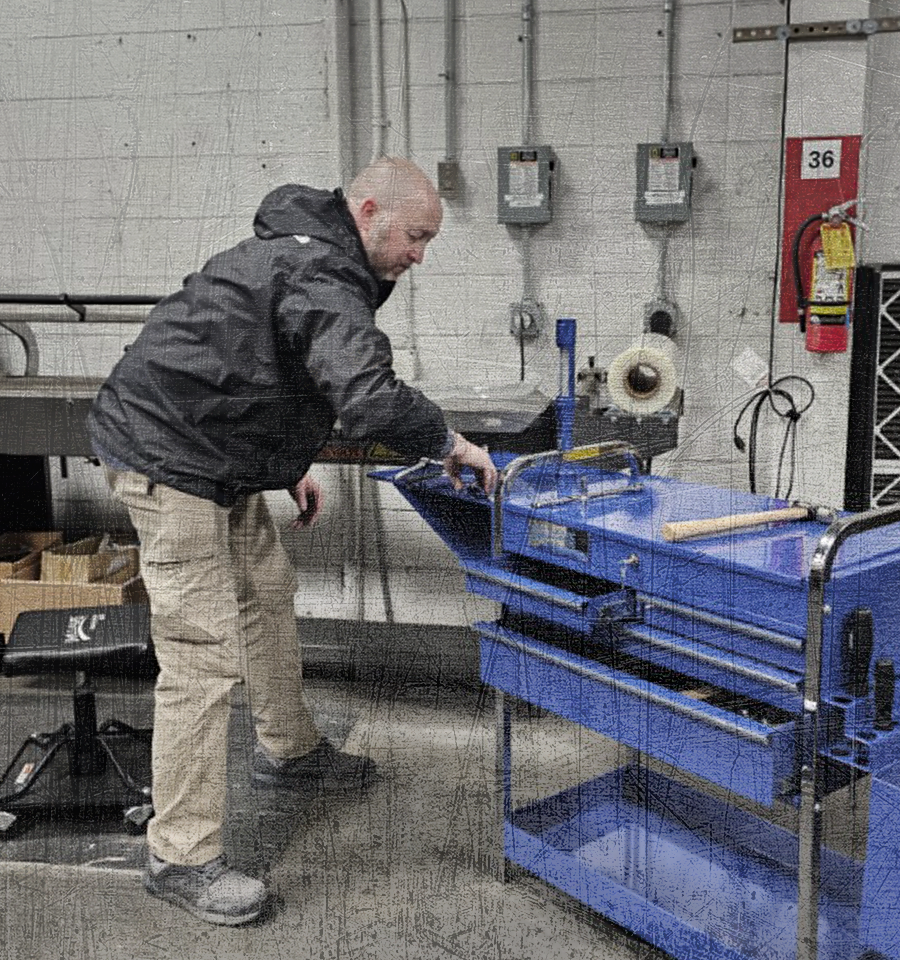
Customer Success - Cart of Gold: Streamlining Repairs in Warehouse Facilities
As more companies move to automate their warehouses and fulfillment centers, 500,000 sq. ft. industrial spaces with hundreds of working robots are becoming more common. These facilities provide new levels of efficiency with a workforce that can operate 24/7, and tool management solutions from Williams can help clear hurdles to further streamlining operations.
When a robot is not working, fixing it comes with some logistical challenges. Maintenance shops usually have a central location, but getting to the place where a repair is needed can still require a long trip across the warehouse. The areas where robots are in operation are often congested with large expensive equipment, making driving a cart to the malfunctioning machine or moving it to a more convenient location nearly impossible. As a result of these circumstances, a technician will usually walk to the robot, carry their tools, and work on it at the station.
With the sprawling distance between the maintenance offices and the machines that need servicing, technicians want to bring all the tools in one trip. However, the tight spaces limit the size of tool carts, and tool bags quickly get heavy and overfilled when the technician brings everything they could need.
After studying the process of traveling to and completing a maintenance job, the Williams territory manager worked with a major fulfillment chain to develop a push tool cart specific to these applications. The frame is no larger than another person, giving the technician flexibility to navigate it through tight work areas. Instead of focusing on making the shelves longer and wider, this design utilizes vertical space. Each cart is equipped with multiple levels of shelves to maximize storage, holding up to 300 tools in a single cart.
In addition to increasing the number of tools technicians can transport at once, this design improves organization. Fixing robots requires precision. A tool that almost fits will not be good enough. Imagine the frustration of a technician who walked all the way across the facility to the robot they need to fix, only to realize they forgot the right sized wrench. Williams’ carts include laser-etched foam cutouts of all the tools a worker would use on the job site. Not only does this help ensure the full set is available when needed, but it also provides an easy system to prevent tools from going missing.
Every mechanic knows that the right tool can make all the difference in getting the job done. Sometimes, that tool is a specially designed cart from a partner like Williams that understands the needs of the operation. Contact us today to get started.